First off, Ameliorative Bottom Line (ABL) will never stop trying to become qualified for Its’ Clientele. We’re always looking for solutions, for your Bottom Line focused ROI. ABL’s Goals; has helped companies achieve their Goals!
With this said, do yourself a quick favor. Find what’s the psychological need; for a human being, to hear that they are “Appreciated ? ” (Appreciation from Employer)
As your thinking about it, think about this.
How much money have you spent, doesn’t matter what project, you could have done these projects for only a 10th of the cost, if you had contracted ABL for Leadership AEP.
Why ABL AEP works. Ameliorative and Transformative Paradigms Go to paragraph “Organizational Transformation” pg.332
(Scroll Down)
Become the Desirable Supply Chain Source
( SCROLL DOWN )
It’s essential to remember that what consulting firm’s rarely layout for you is “YOUR Actual Problem,” they’ll stick to the technical aspects your employees will need, and avoid your internal issues altogether.
ABL focus is to work with you as a Business Analyst as a Partner.
Focused on tackling your issues, present the solution, draw-up the case study to instruct and develop in-house the proactive Continual Improvement process to capture similar and future issues. That’s the Bottom Line ROI.
In reference to Wall Street, Industries Criticism of Consultants, I’m in agreement.
A great number of consulting firms, many of which claim expertise in Six Sigma when they have only a rudimentary understanding of the tools and techniques involved. Also, Lack of Knowledge of the market or industries of their client.
This is the reason why ABL’s “Vision of Purpose,” ABL’s creation of “Disciplined Agile Manufacturing” and Tailored to Your “WOW” works ! (Purpose Statement, or in ABL AEP I or II pg. 6, pg. 8 Jason Jennings, pg. 9-13, pg. 18 and pg. 20)
Consulting Firms DO NOT do this, Especially for a SMALL or MEDIUM sized company. They never heard of Disciplined Agile Manufacturing or AEP !
NOBODY SPENDS THE NEEDED TIME AND EXTRA WORK TO DO THE JOB CORRECTLY, FOR … “TRANSFORMATIVE POWER; SUSTAINING EXTRAORDINARY RESULTS.”
SOUNDS LIKE A GRANDIOSE PIPE DREAM !!
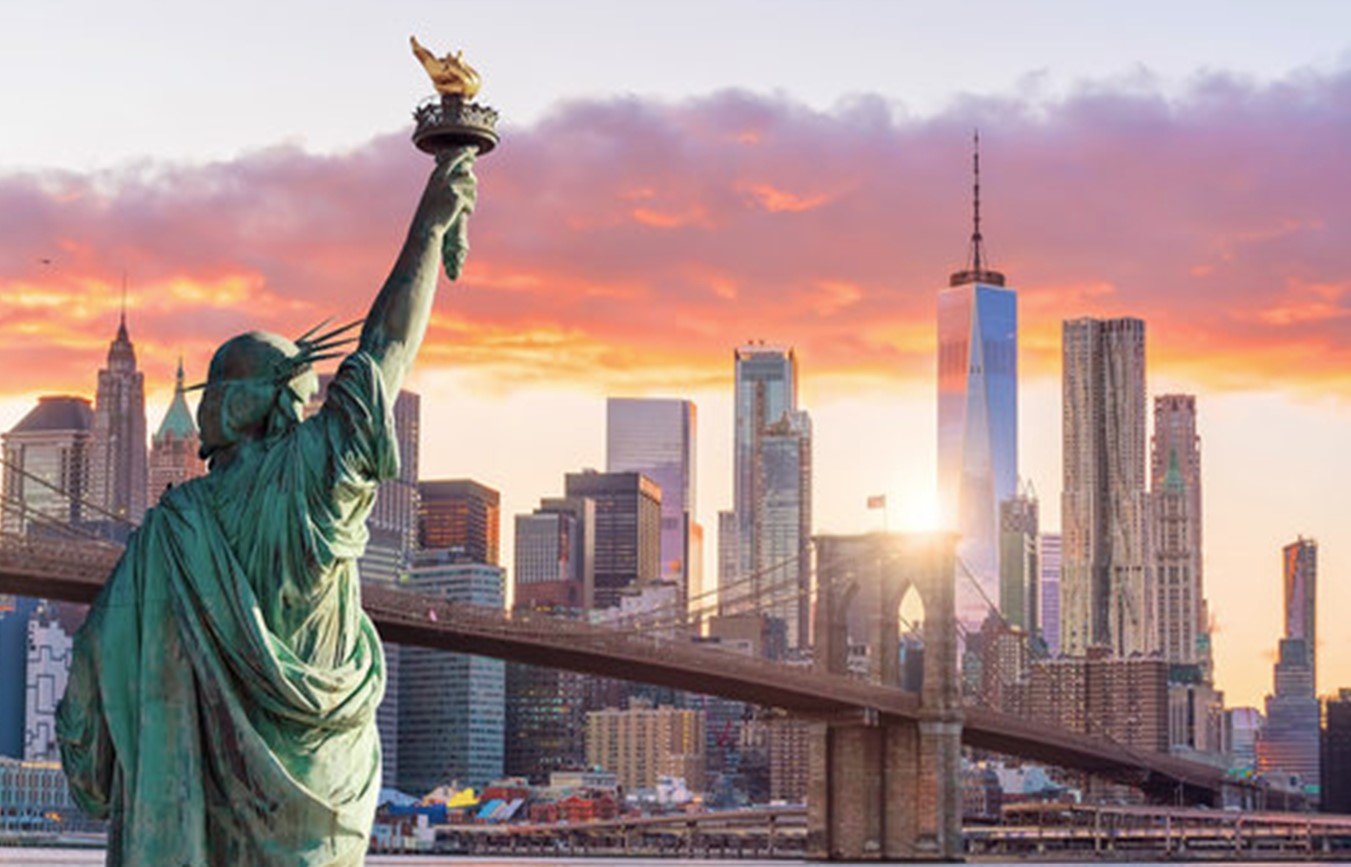
Before the Information Age in the late 20th century, businesses sometimes laboriously collected data from non-automated sources. As they lacked computing resources to analyze the data properly, they often made commercial decisions primarily by intuition.
Now, we are in the Forth Industrial revolution, called Industry 4.0 Digital Manufacturing Operational Excellence. Included with-in this is CSR Corporate Social Responsibility. 4.0 Operational Excellence foundation is built on AEP Accountability and Empowerment; holding you accountable for the continuous improvement of your work force. Click this… Why You! page 3 find out.
As businesses started automating their processes, the availability of data increased. However, collection often remained a challenge due to a lack of infrastructure for data exchange or incompatibilities between systems. Reports on the gathered data sometimes took months to generate and these delays allowed lack of informed strategic decision-making.
The result is now customers and supply chains demanding value-added benefits from your products and service.
The advent of increasing standards, automation, and technologies led to vast amounts of data becoming available. Data warehouse technologies allowed the building of repositories to store this data. Improved enterprise application integration tools have increased the timely collection of data. OLAP reporting technologies allowed faster generation of new reports which analyze the data. As of 2010, business intelligence has become the art of collecting large amounts of data, extracting useful information, and turning that information into actionable knowledge.
Our AEP solution is the key determinant foundation of success, longevity and durability; to your Organization.
Various frameworks for implementing business performance management exist. Companies use a top-down framework to align planning and execution, strategy and tactics, and business-unit and enterprise objectives. Reaction frameworks include the Six Sigma strategy, Balanced Scorecard, Activity-Based Costing (ABC), Objectives and Key Results (OKR), Total Quality Management (TQM), Economic Value-Add, Integrated Strategic Measurement, and Theory of Constraints (TOC). All of these fall under the KAIZEN Methodology, they are it’s principals and tools. But KAIZEN’s purpose is plan ahead be informed of impeding changes; Not reactionary, it’s “Continual” Improvement. Today’s requirement is that the operators and technicians are methodical trained by AEP for Digital Manufacturing/ LEAN/ Continual Improvement Agility.
Enterprise Leadership Development
AEP Accountability & Empowerment Paradigm Disciplined Agile Manufacturing
AEP— Development: To become, nimble self-organized cross-functional employees for individual and group applications & scaled to agile framework for your ( Tailored ) “WOW,” YOUR organizations industry processes. (WOW)
Consider
Introductory Instruct Agile Manufacturing, Agile Leadership, Agile Management
or
The Introduction of the “Disciplined” Agile Concept
For true business agility we need to “Choose your Agile Way-of-Working (WOW)”
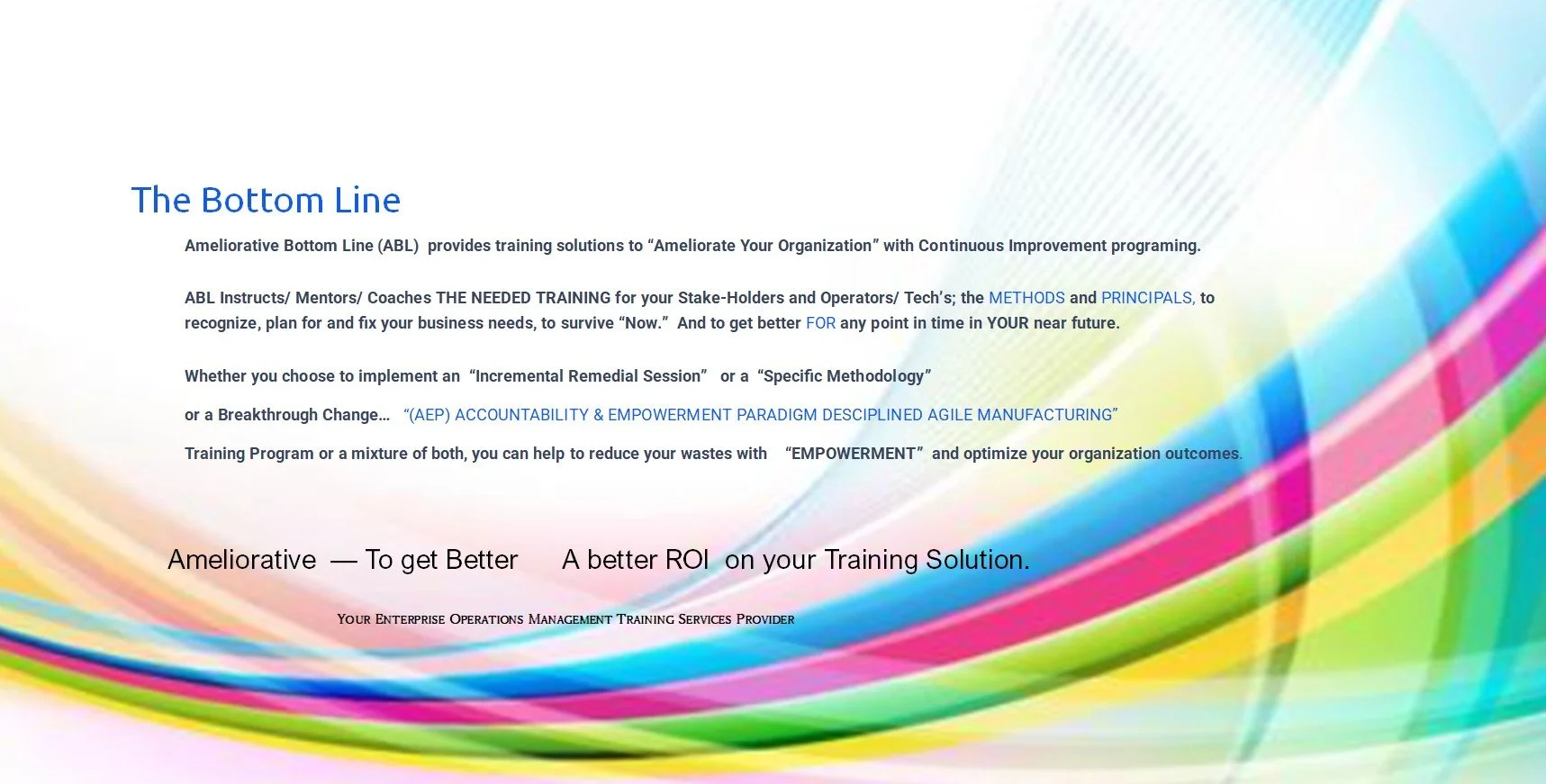
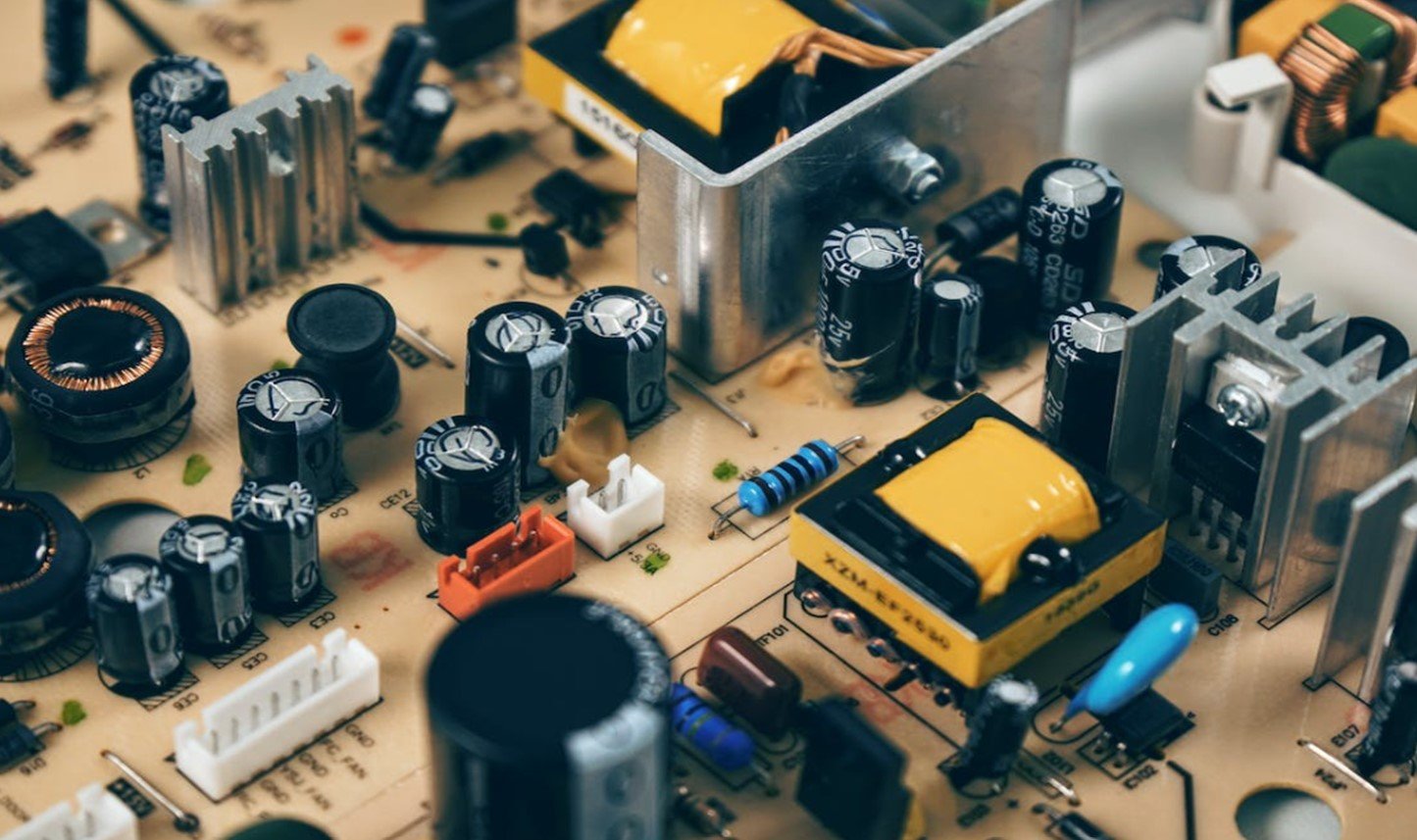
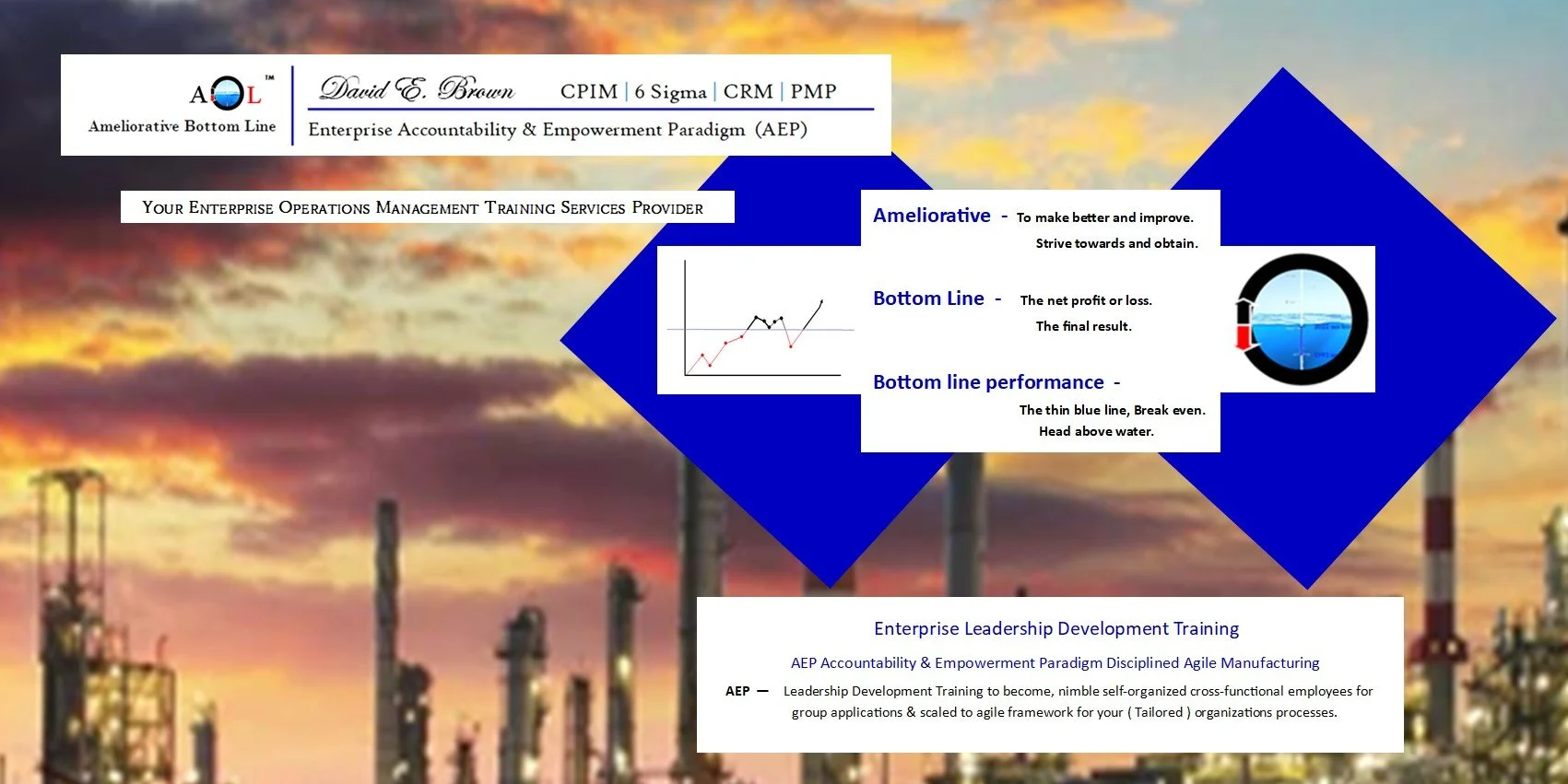